The Drum process
Virgin Plastic
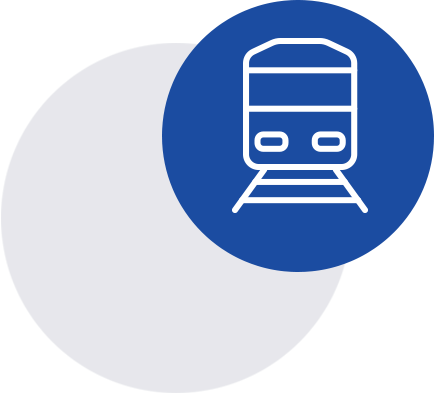
Prime Grade, High Molecular Weight, High Density Polyethylene (HMWHDPE) is single sourced. Utilizing a proprietary gas phase technology natural gas, chemicals and heat are used to produce a high pure, food grade, virgin, natural, HMWHDPE pellet. These pellets are shipped to PolyCube in both rail cars and bulk trucks which are blown or vacuumed into our indoor, dedicated silo storage system.
Melt
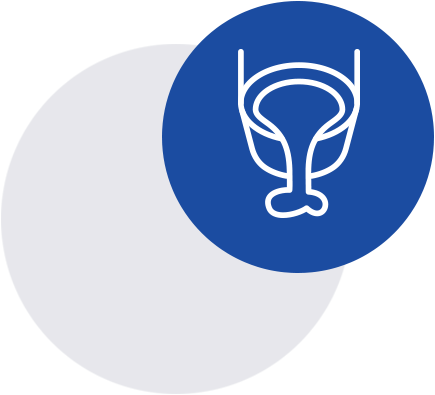
The blended material is gravity fed into the extruder. The extruder is a long metal tube called a barrel with a large metal screw inside. The screw turns, driving the HMWHDPE forward between the narrow gap of the screw flights and the barrel wall. This causes frictional heat and the plastic melts.
Blow Mold
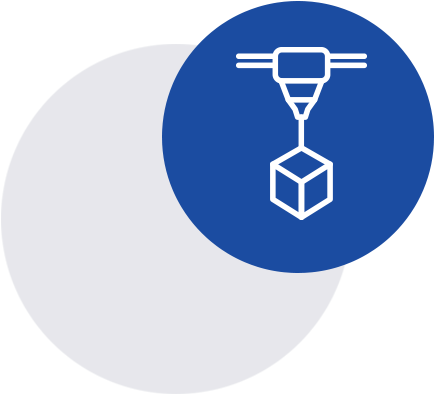
The Parison is then automatically cut from the head into the aluminum mold. The mold automatically closes while blow pins rise from the bottom. While air is blowing through the pins the mold is held tightly closed using hydraulic pressure. Next the Parison is blown into the walls of the mold. Chilled water is being pumped through small capillary tunnels inside the walls of the molds. This process transfers the heat from the plastic to the aluminum molds. The Drum is now formed.
Post Mold Cooling
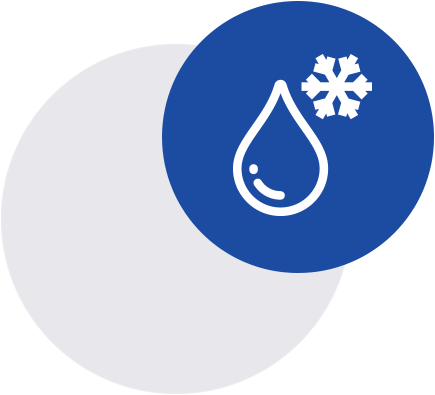
The warm Drum is positively cooled in an additional 16 stations. In these stations the Drums are further cooled using ambient air flow to exchange the warm air with the ambient air in the drum. Since these Drums are open top this works very effectively. This process insures the Drum opening is round and the side walls and bottoms are flat.
Post Manufacturing Quality Control
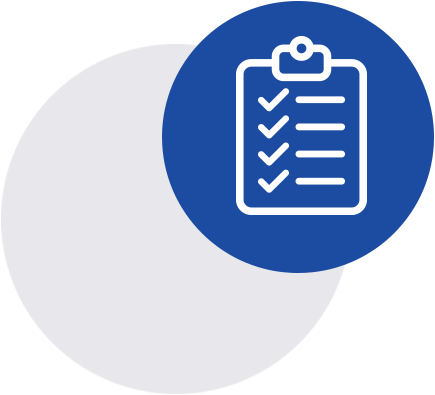
A minimum of 2 Drums per shift are quality checked by a quality trained PolyCube Supervisor Inspector. They complete an extensive written check-list measuring for weight and wall thickness/distribution to insure the Drums are within preset tolerances.. The test sheets are reviewed and maintained by the Operations Manager. Other in house testing performed is a freezer drop. Lastly, official United Nations Department of Transportation testing is done annually to certify each design type by an independent third party DOT approved testing laboratory.

Blend
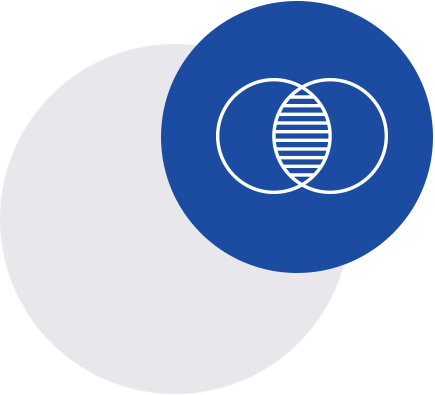
Prior to being vacuumed to the extruder, the HMWHDPE is air conveyed into a Blender / Mixer where precise amounts of colorant and production flash regrind are volumetrically mixed according to an exact computer controlled recipe.
Extrude
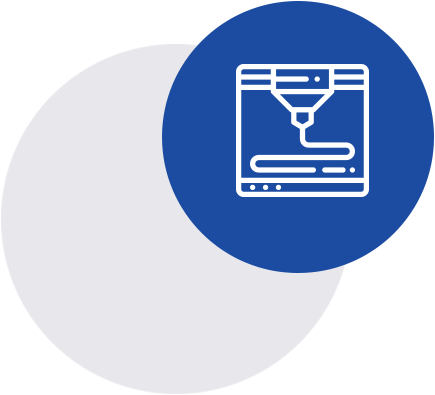
The melted plastic is driven into the Head of the Blow Molder from the extruder. Inside the head are proprietary mechanics and technology that, utilizing a computer generated recipe pre-set by our process engineers, squeezes and shapes the plastic into a tube called the Parison. This insures the exact and correct amounts of plastic are in the right parts of the Parison so when in the mold the Drum will have precise wall distribution.
De-flashing
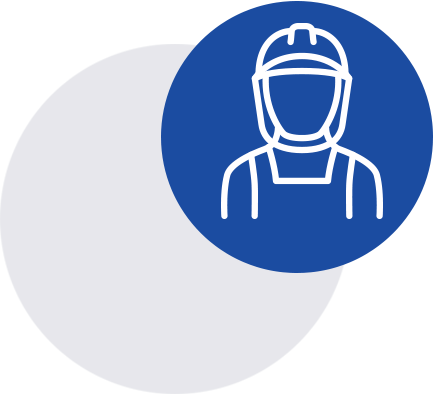
Once the molding process is complete, the molds release their air and hydraulic pressure. The formed Drum is mechanically removed from the mold. The flash and excess plastic is precisely removed by an operator trained in this process. The flash is conveyed into a grinder for reprocessing.
Visual Inspection / Lidding / Inventory
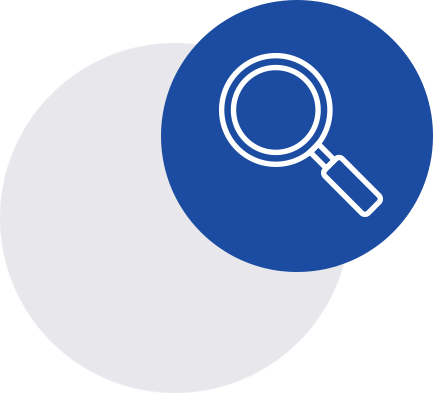
Lastly there is a final Blow Mold Operator light inspection of the Drum for any visual defects such as carbon spots or open welds. If the operator determines the Drum meets the entire quality standard then he closes the drum with a metal locking ring and plastic cover.The drum is than transported into the general drum inventory ready for customer shipment. Any Drums failing the inspection process are cut and conveyed into the grinder for reprocessing.
See why our customers think we are A BETTER WAY.
Polycube offers a wide variety of product options with customized volume commitments to meet our needs. As a regional distributor, Polycube has allowed us to build a new and more diverse customer base in the HD Tighthead market thanks to their ease of doing business.
Ryan E. Brown
Working in the industrial rigid packaging distribution industry, The Polycube Company’s entrance into the small closed head HDPE pail market was like a breath of fresh air. They have set themselves apart from the competition with their investment in cutting edge technology and a commitment to quality unlike any other OEM in the US, but perhaps their greatest asset is their unwavering dedication to total customer satisfaction.
Christopher Evoy
Working with The PolyCube Company has been great – any questions or issues are quickly and easily address and resolved. Their entire team is very responsive and truly a pleasure to work with!
Michelle Coppedge
As head of Purchasing for Warsaw Chemical, I have single source purchased my 20-liter tight head containers from The PolyCube Company in Levittown PA since 2017. Our company specifications require a very exact and heavier gram weight. Due to PC’s state of the art technologies they have been able to meet these requirements without exception. PC committed to an inventory program for Warsaw and they have never let us down on a delivery date despite our ever changing scheduling requirements. PC does all this for us with transparency and ease. I think they accomplish this because they have an exceptional team in their sales, customer service and production departments. They always make me feel like the most important customer.